The efficient cleaning of fleets requires careful consideration of the appropriate chemicals and techniques. Selecting the wrong chemical can result in ineffective cleaning, while an incorrect detergent amount can impact performance. To ensure optimal outcomes, it is crucial to engage in a discussion with the chemical supplier regarding the washing process.
The dilution ratio assumes great significance, particularly in touchless cleaning, and it is advisable to avoid caustic-based cleaners. Dwell time and chemical reaction are also essential factors to contemplate, as they allow detergents to effectively penetrate and emulsify grime and dirt. Increasing dwell time on vertical surfaces can be achieved through the use of foam, and the choice of spraying system should be contingent upon the washing conditions.
The selection between a one-step, double-step, or two-step process is contingent upon specific needs, with the two-step process often yielding superior results. Furthermore, hot water facilitates rapid and efficient cleaning, while soft water enhances cleaning efficiency compared to hard water. Given the physically demanding nature of efficient fleet washing, teamwork is essential, especially for large contracts, as it necessitates prompt rinsing, soap spraying, and brushing.
Key Takeaways
- Using the right chemical and amount is crucial for effective fleet washing. It is important to discuss the washing process with the chemical supplier to ensure the best results.
- Dwell time and chemical reaction play a significant role in cleaning performance. Allowing detergents enough time to penetrate and emulsify grime and dirt improves cleaning effectiveness.
- Different washing processes, such as one-step, double-step, and two-step, can be used for fleet washing. The combination of multiple detergents can enhance cleaning performance.
- Hot water provides rapid and efficient cleaning, especially in winter. Cold water can be used during summer months when vehicle surfaces are already hot. Soft water is also advantageous for pressure washing as it improves cleaning efficiency compared to hard water.
Chemical Importance
The pre-existing knowledge emphasizes the importance of using the right chemical and amount for efficient fleet washing. Using the wrong chemical can lead to ineffective cleaning, while an incorrect detergent amount can affect cleaning performance.
Chemical selection plays a crucial role in achieving optimal cleaning results. It is essential to discuss the washing process with the chemical supplier to determine the best chemical for the specific fleet washing needs.
Additionally, the dilution ratio is a critical factor in touchless cleaning. Properly diluting the detergent ensures effective cleaning without causing any damage to the vehicle surfaces. Achieving the correct dilution ratio requires careful consideration of the detergent’s concentration and the water volume used for washing.
By selecting the appropriate chemical and maintaining the right dilution ratio, fleet operators can ensure efficient and effective cleaning of their vehicles.
Dwell Time/Chemical Reaction Time
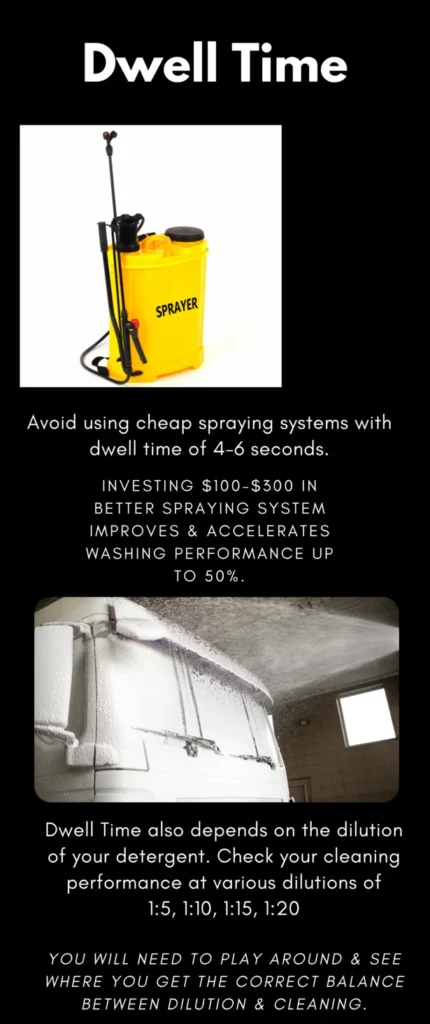
Longer dwell times greatly enhance the cleaning performance of detergents, increasing the chance of effectively removing grime and dirt from fleet vehicles.
The dwell time refers to the period in which the detergent is allowed to penetrate and emulsify the dirt and grime on the vehicle surface.
Foam plays a crucial role in extending the dwell time on vertical surfaces, as it clings to the surface and prevents the detergent from quickly running off.
Factors that affect the dwell time in fleet washing include the type of spraying system used and the weather conditions.
It is important to choose a spraying system that can provide adequate coverage and ensure that the detergent has enough time to work.
However, it should be noted that foam cannons may not be suitable for cold weather conditions, as the foam may freeze before it has a chance to effectively clean the vehicle surface.
One-Step, Double-Step, Two-Step Process
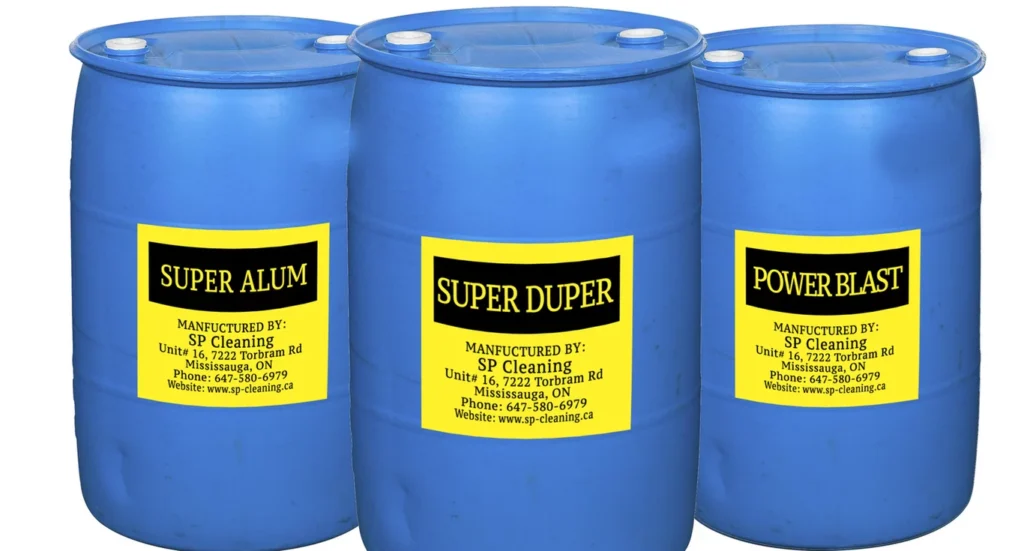
One method for fleet washing involves using a single detergent, while another method involves using multiple detergents in a specific sequence.
Benefits of One-Step Process:
- Simplicity: The one-step method simplifies the fleet washing process by using a single detergent for all cleaning. This reduces the need for multiple products and streamlines the washing procedure.
- Time Efficiency: With only one detergent to apply, the one-step process saves time compared to the double-step and two-step methods. This is especially beneficial for large fleet washing contracts, where time is of the essence.
Comparison of Double-Step and Two-Step Methods:
- Double-Step Process: This method involves using a pre-soak degreasing detergent followed by a multipurpose detergent. It provides enhanced cleaning power by targeting specific contaminants and improving overall cleaning performance.
- Two-Step Process: In this method, an acidic detergent is first used to remove tough stains and grime, followed by an alkaline detergent for thorough cleaning. The two-step process is effective for heavily soiled fleets, providing a comprehensive cleaning solution.
The Two-Step Process is a good technique to use particularly on trailers, or dull-looking metallic parts of a truck tractor. Used at correct concentrations, it helps break the bond between the road film and the surface and accelerates the washing process. SP Cleaning’s touchless detergents can be used in the Two-Step washing process.
Hot Water vs Cold Water
Hot water and cold water are both viable options for fleet washing, with each having its own advantages and considerations.
When it comes to fleet cleaning, hot water offers several benefits. Firstly, hot water provides a more rapid and efficient cleaning process compared to cold water. This is especially important for year-round washing, particularly in winter when the temperature drops. Additionally, hot water is essential for commercial pressure washing, as it ensures thorough cleaning of fleet vehicles.
On the other hand, cold water can be used during the summer months when vehicle surfaces are already hot, saving energy and reducing costs.
It is important to note that commercial detergents work in both soft and hard water conditions, making it possible to achieve efficient fleet washing with either hot or cold water.
Soft Water vs Hard Water
Soft water and hard water have different effects on the efficiency of the cleaning process due to the mineral content present in hard water. Here are some key points to consider regarding soft water and hard water in fleet washing:
- Benefits of soft water:
- Soft water improves cleaning efficiency compared to hard water.
- It does not contain the minerals that leave behind limescale residue and decrease soap efficiency.
- Commercial detergents work well in both soft and hard water conditions, but soft water is particularly advantageous in rural areas with well water.
- Water hardness test:
- Determining the hardness of the water is essential in fleet washing.
- A water hardness test can help identify the need for using soft water.
- If the water is hard, it may be necessary to use water softening methods or equipment to improve cleaning efficiency.
- Soft water for pressure washing:
- Soft water is especially beneficial for pressure washing.
- Its ability to increase soap efficiency and prevent limescale residue ensures thorough cleaning of fleet vehicles.
- Commercial detergent compatibility:
- Commercial detergents are designed to work effectively in both soft and hard water conditions.
- This versatility allows for consistent cleaning performance, regardless of the water hardness.
1 Person vs 2 People vs 3 People Team
If you are targeting to land a big fleet washing contract, you will need a team of at least 2 people. Washing fleet is a physically demanding task and requires you to spray soap, brush heavily soiled areas and rinse promptly.
Big fleet washing contracts sometimes require a bigger team. In a 3 people team; one person sprays the soap, the second person does the brushing and the third person rinses. They switch roles every hour or so; distribute work evenly and avoid fatigue.
Fleet washing team needed. Physically demanding. Roles rotate. Avoid fatigue.
Brushing vs Touchless Washing
Touchless Washing is doable, it definitely is, about 80-90% of the time. Right detergents, well-maintained equipment, and a hardworking team can deliver touchless washing. But even that team will carry a brush with them to a job site. You can’t go to a fleet washing job and not carry a soft brush with you.
Tough soils or neglected fleets sometimes require mechanical agitation, so you gotta apply the brush. An experienced pressure wash operator can spot these areas on a truck and selectively brush those areas.
At SP Cleaning, we are committed to our mission to help local pressure-washing businesses achieve high-performance touchless washing. We strongly believe that these techniques will help you to reach that golden 80-90% touchless cleaning.